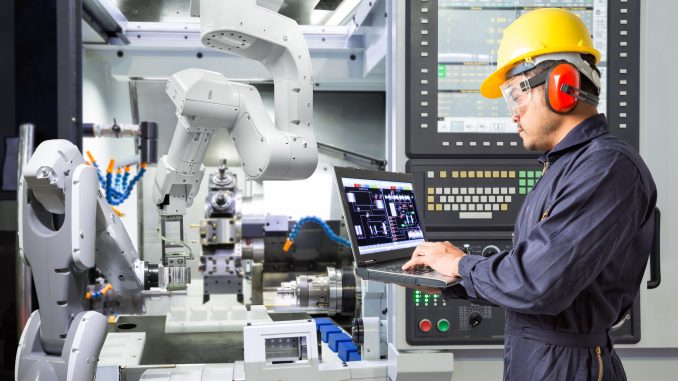
The increasing presence of industrial robots in the workplace has raised safety concerns. With their ability to move quickly and accurately, they can present a risk if not managed properly. To ensure safe use of these robots, it is important to have standards for robot safety that are followed by employers and employees alike. This article will examine the importance of having robot safety standards and discuss how they can be implemented to create a safer environment for workers.
Introduction to Robot Safety Standards
Robot safety standards are guidelines which set out requirements for using robots safely in industrial settings. These regulations cover topics such as training, maintenance, installation and operational procedures necessary for safely operating robots in the workplace. They also provide guidance on how to protect personnel from potential hazards associated with robotics operation, including noise levels, hazardous fumes or other environmental factors. Additionally, many countries require companies to comply with national laws regarding workplace health and safety when deploying robotic systems.
Regulations And Guidelines
In the industrial workplace, it is essential to ensure that robots are used safely and efficiently. To accomplish this goal, there are various regulations and guidelines in place to protect both human workers and robotic technology from harm or injury. In order for a robot system to be approved for use in an industrial setting, the manufacturer must provide evidence of compliance with local safety standards set out by governing bodies like OSHA (Occupational Safety & Health Administration).
Training Requirements
With the increase in industrial robotics, safety concerns have become paramount. To ensure safe use of robots in the workplace, it is essential to employ comprehensive training requirements for workers who interact with these machines. Training should cover basic robot operational principles as well as potential hazards and how to mitigate them. This includes proper handling when setting up or repairing a robot, understanding all safety systems and controls on the machine, and being aware of any risks associated with specific tasks. It is also important that employees receive refresher courses regularly to stay updated on new technologies and changes in regulations related to robotic operations.
Risk Mitigation Strategies
Risk mitigation strategies are essential for the safe use of industrial robots in the workplace. The most widely accepted strategy is to identify potential risks and assess their severity before allowing a robot to be used in any environment, especially when first introduced. This includes evaluating hazards associated with robotic movements and investigating sources of energy that can cause harm if not properly managed. Additionally, it is important to ensure personnel safety by providing adequate training on appropriate robot operation procedures and protective equipment such as gloves, face shields, or visors.
Conclusion
Robot safety standards are essential for ensuring safe use of industrial robots in the workplace. Proper implementation and adherence to these regulations can help reduce potential risks associated with the operation of such machinery, while also improving overall efficiency. Regulations and guidelines must be developed that clearly outline the operations and maintenance requirements related to the specific robot being used. In addition, training requirements should be established so workers have a clear understanding of how to safely operate the robot. Risk mitigation strategies must also be implemented which proactively identify any potential hazards before they occur and include measures such as regular inspections, preventive maintenance procedures, and emergency shutdown protocols.